Reference PROJECTS
Digital Twin Implementation with High-Fidelity Process Simulation
Project details
Project details
Client
Top Pharma Client
Location
Sweden
Market
Medtech
Solutions we provided
Digital twin of the novel spray drying process which Keyplants Automation delivered the automation system for. Virtual replica of the process- and batch control system fully integrated with a high-fidelity process simulation.
Executive Summary
Executive Summary
A leading pharmaceutical manufacturer faced critical time-to-market pressures for new drugs produced with a novel spray drying process, compounded by the sequential nature of traditional system development. We implemented a high-fidelity digital twin of their new production system, built on Siemens SIMIT with integrated custom process models, programmed in C#. This virtual replica achieved seamless, full integration with the PCS7 control system and batch execution logic. This enabled parallel automation development, comprehensive virtual FAT/SAT, and realistic operator training well before facility completion. Crucially, the digital twin also allowed for full process simulation and parameter tuning, facilitating data-driven decisions to optimize process recipes and drastically reducing the number of physical tests required to find parameters which yielded the optimal product. The project significantly compressed timelines, enhanced operator readiness, and optimized process performance from day one. This case study demonstrates how digital twins drive efficiency and agility in pharmaceutical manufacturing.
Understanding Digital Twins
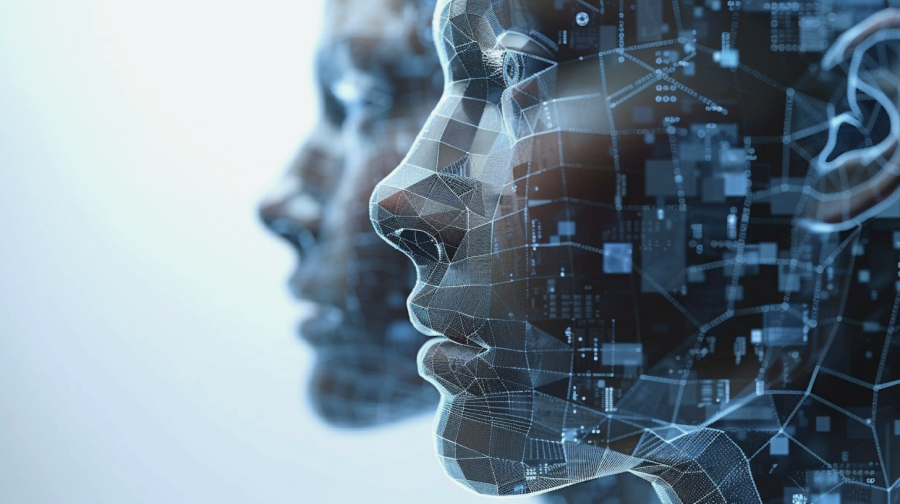
Pharmaceutical manufacturing demands speed and quality. Pharma 4.0 leverages advanced technologies like the digital twin to meet these demands. A digital twin is a dynamic, high-fidelity virtual replica of a physical process or system. It allows for real-time monitoring, analysis, and prediction, offering significant advantages, especially for new system or process development:
Accelerated Development & Time-to-Market: Digital twins enable virtual testing of complex systems and control strategies before physical installation. This dramatically shortens design and validation, leading to faster time-to-production and quicker time-to-market for critical drugs.
Reduced Risk & Optimized Design: By simulating complex physics and chemistry, digital twins predict product behavior and quality. This identifies potential issues early, leading to more robust, optimized designs and mitigating risks associated with new implementations.
Enhanced Operator Training: Digital twins provide a safe, realistic virtual environment for operator training and onboarding. Operators gain hands-on experience without impacting live production or waiting for facility completion, significantly reducing the learning curve.
Decoupled Project Timelines: Digital twins allow parallel execution of critical tasks. Automation engineers can develop and test control software against the virtual replica before physical machinery is ready. This decoupling of dependencies, especially between site progress and subcontractors, enables a tighter project execution timeline.
Streamlined Testing & Validation: Extensive internal testing, Factory Acceptance Testing (FAT), and Site Acceptance Testing (SAT) for software can be conducted against the virtual twin. This ensures thoroughness and accuracy independently of the physical plant's readiness.
Digital twins provide the agility and efficiency, essential for competitive markets and modern pharmaceutical innovation.
Challenge
A top pharmaceutical manufacturer faced a complex project: developing a cutting-edge production system for a new type of spray drying. This intricate process demanded precise control and a deep understanding of reaction dynamics to ensure product quality.
The primary challenge was the sequential nature of traditional project execution, involving facility construction, equipment installation, automation development, and validation phases. This approach resulted in significant lead times, risking delays in bringing new products to market. They needed a method to compress this timeline, mitigate risks, and simultaneously enable process experimentation to tune parameters for rapid operational readiness.
Our Solution
Our goal was a virtual replica capable of simulating complex physics and chemistry to accurately predict product behavior and quality. The solution utilized Siemens SIMIT as the core simulation platform, but with full integration of the PCS7 control system and batch execution logic. We developed and integrated custom-built simulation components into SIMIT. These components performed complex calculations based on equations rigorously tested and validated by the client's lab engineers and process experts, ensuring high predictive accuracy for the real process.
Key aspects of the project:
High-Fidelity Process Simulation: The digital twin accurately modeled the complex spray-drying process, incorporating a sophisticated thermodynamic mathematical model for real-time process value calculation. This allowed our engineers and the client's process experts to refine and optimize the process early, with confidence in the simulated outcomes.
Integrated Control System Development and Validation: Developed in parallel with the PCS7 control system, the digital twin enabled our automation engineers to perform comprehensive internal testing and validation of the entire control system software against the virtual replica. This was done long before any physical equipment was available, fundamentally changing the development timeline.
Virtual Operator Training: The integrated digital twin served as a highly realistic platform for operator training while the facility was under construction. This allowed operators to gain hands-on proficiency in a risk-free virtual environment without occupying the physical asset.
Decoupled FAT/SAT: The fully integrated virtual replica enabled virtual Factory Acceptance Testing (FAT) and Site Acceptance Testing (SAT) of the control software. This significantly decoupled dependencies between site progress and multiple subcontractors, streamlining the project timeline and ensuring software readiness independent of hardware installation.
Collaborative Approach: We collaborated closely with the client's Subject Matter Experts (SMEs) and stakeholders. Our strategic Pharma Partnership with Siemens also facilitated close work with their experts for optimal SIMIT implementation and control system integration.
Results and Benefits
The digital twin implementation delivered significant, quantifiable benefits, largely due to its deep integration with the control system and high-fidelity process modeling:
Accelerated Time-to-Production & Time-to-Market: Parallel development and virtual testing of the entire control system dramatically compressed the project timeline, leading to faster commissioning and qualification. This was significantly aided by the ability to virtually refine process parameters and optimize recipes, drastically reducing the number of physical tests required once the system became operational.
Reduced Physical Testing & Validation: The digital twin enabled extensive virtual experimentation and test planning. This allowed for better, more realistic predictions of process outcomes, narrowing down the final parameters and recipes to test on the physical system. This reduced the need for physical testing time, eliminating lengthy on-site tests during commissioning.
Enhanced Operator Readiness: Virtual training on the integrated system ensured operators were proficient with the new system before facility operation, significantly reducing ramp-up time and ensuring a smooth transition to production.
Optimized Process Performance: High-fidelity simulation and its integration with control strategies allowed proactive identification and optimization of process parameters, ensuring optimal performance and consistent product quality from day one.
Cost Savings & Risk Mitigation: Identifying and resolving complex control and process interaction issues virtually, alongside the reduced need for extensive physical testing, avoided costly rework, delays, and potential production losses in the real world.
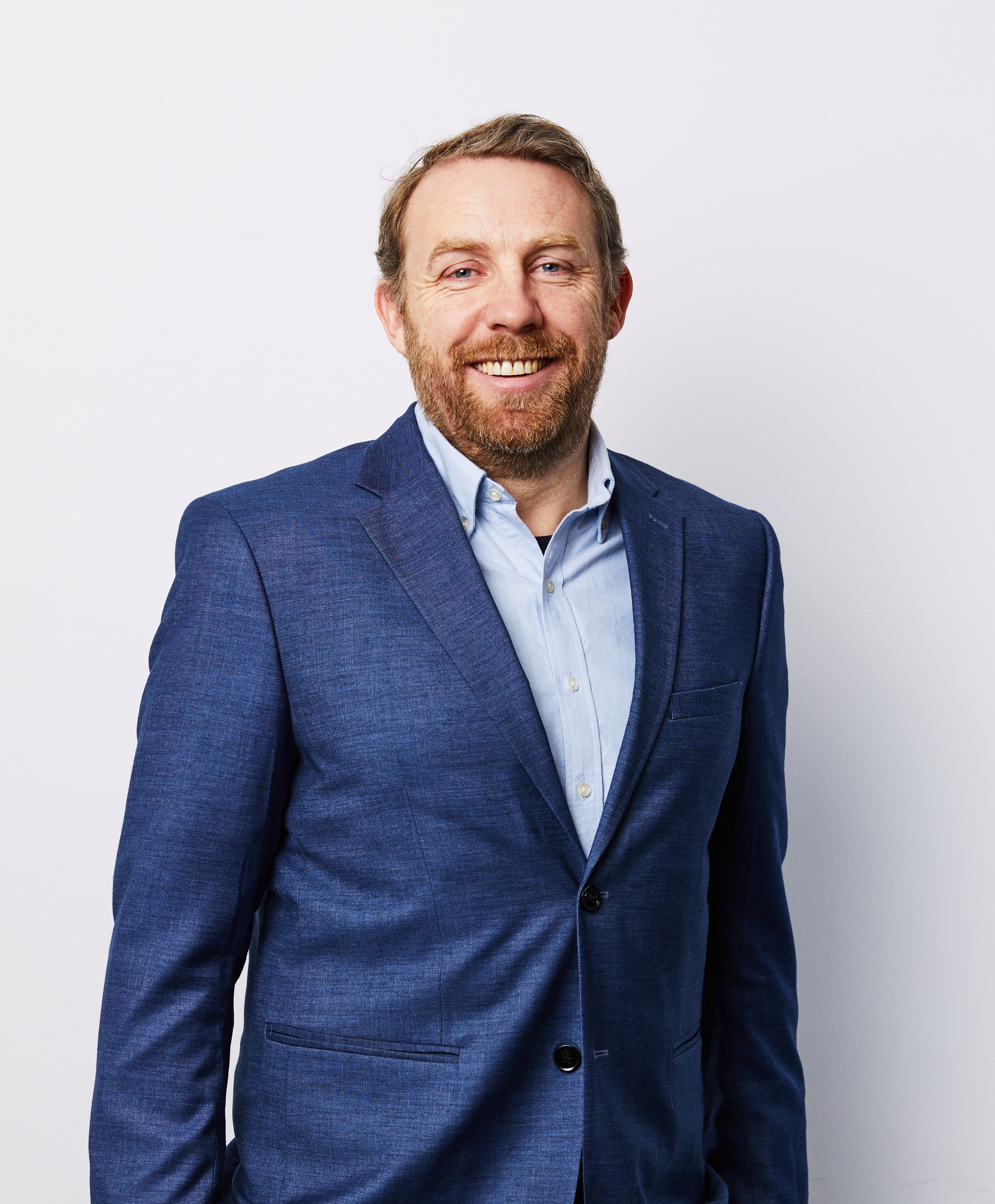
Key Learnings and Future Outlook
This project highlighted the transformative potential of Pharma 4.0. Key learnings included the critical importance of deep collaboration between client subject matter experts and automation engineers, and leveraging strategic technology partnerships.
Moving forward, the digital twin remains a cornerstone for the manufacturer's operational excellence. We are currently initiating a project to further enhance system fidelity by integrating gProms, which will expand its capabilities for continuous process optimization and to predict quality outcomes of new products introduced through this process – reducing the need for unproductive down time to run tests. We continue to develop scalable digital twin solutions, empowering manufacturers with efficiency and agility.
